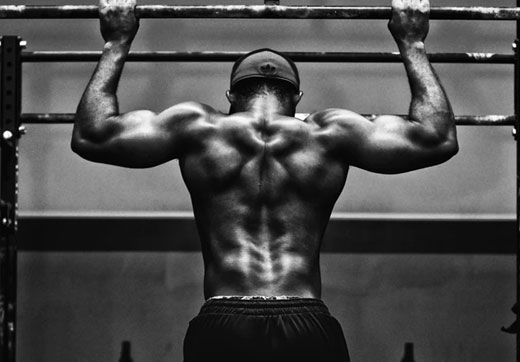
Compressive vs. Flexural Strength
At Semco, we think of ourselves as master problem solvers. Since we take the utmost care in the machining of graphite materials, we often find that problems reported by our customers, under careful investigation, turn up issues not related to the quality of the graphite components we machined. Just because we are confident in our product doesn’t mean we stop investigating, though. On the contrary--we want our customers to get the most out of their graphite components. If they are not working properly, or breaking, we will help the customer get to the bottom of the issue, whether or not that issue involves the quality of the graphite components in question. Here, we’d like to demonstrate, through a recent example, the care we take to assist our customers when they contact us about a problem with graphite components, in this case, graphite plates we manufactured which were continually breaking. The thorough detective work of our experienced engineers found the bug in the system and got this customer’s assembly humming again.
Identifying the Issue: Materials or Assembly?
Recently, a customer of ours reported that a series of graphite plates used in a bell furnace kept breaking. This particular furnace uses a series of flat discs sandwiched together between a couple of steel plates. Pressure is applied on the discs through a rod running through the middle of the plates and torqued with a bolt to a value that does not exceed the compressive strength of the material. In our first conversations with this customer about the problem, they stated that nothing had changed in their process and the bolts were torqued to the same spec. Yet, one furnace continued to have graphite disc failures. As in most cases, although a series of furnaces were in use, only one had disc failures. Usually, what this means is that the problem lies not with the graphite components but with the particular assembly. Still, we had to cover all our bases and rule out problems with the graphite plates. On our visit to the facility, we observed that, indeed, the procedure of assembling the tooling in the furnaces was followed consistently throughout all their furnaces. We asked if the steel fixtures are specific to each furnace, and it was confirmed that they are. Our initial thought was to swap the steel plates and run the furnace with steel plates from a different furnace, since they are interchangeable. With the alternate set of steel plates, they executed one run flawlessly. No graphite plates broke. Our hunch about the steel plates being the problem was now closer to a theory, but one we would need to test back at our facility.
Semco Experts Find The Solution
We asked the customer to ship the original set of steel plates so that we could take a closer look at them. Once the plates arrived at our facility, we immediately checked the flatness on these plates. They were supposed to be within 0.010.’’ In actuality, they were over 0.200,’’ with certain spots likely damaged by tooling used in the assembly process. Put simply, there were high and low spots on the plates. In a system designed to function as a tight assembly, with no gaps between plates, such irregularities can spell disaster. The defects created gaps between the steel and graphite plates, allowing the graphite to flex ever so slightly. In effect, the values calculated as compressive strength values were actually flexural strength values, meaning there wasn’t just compression, but also slight bending, happening to the graphite material. Since flexural strength values are roughly half that of compressive strength values in graphite, the graphite components experienced much greater stress than they were manufactured to withstand.
Once we affirmed our initial suspicion about the steel plates, the solution was simple. The steel plates were ground flat (within 0.010’’). Put back in operation, the furnace performed to spec with no further graphite failures. Once again, problem solved.